I always like how the 1953 corvettes seats look like they where part of the car. The seats that I choose looked a little small in the truck cab so I came up with the idea that I would make a surround around the seats to make them look like they where part of the cab. Chris and I decided that making it out of metal would be a pretty complex project. The next best material I came up with is fiberglass. It had been about thirty years ago since I have done any work with fiberglass and said to myself I can do this. The project began with a lot of research on the Web and the trusted YouTube on how to make the forms.
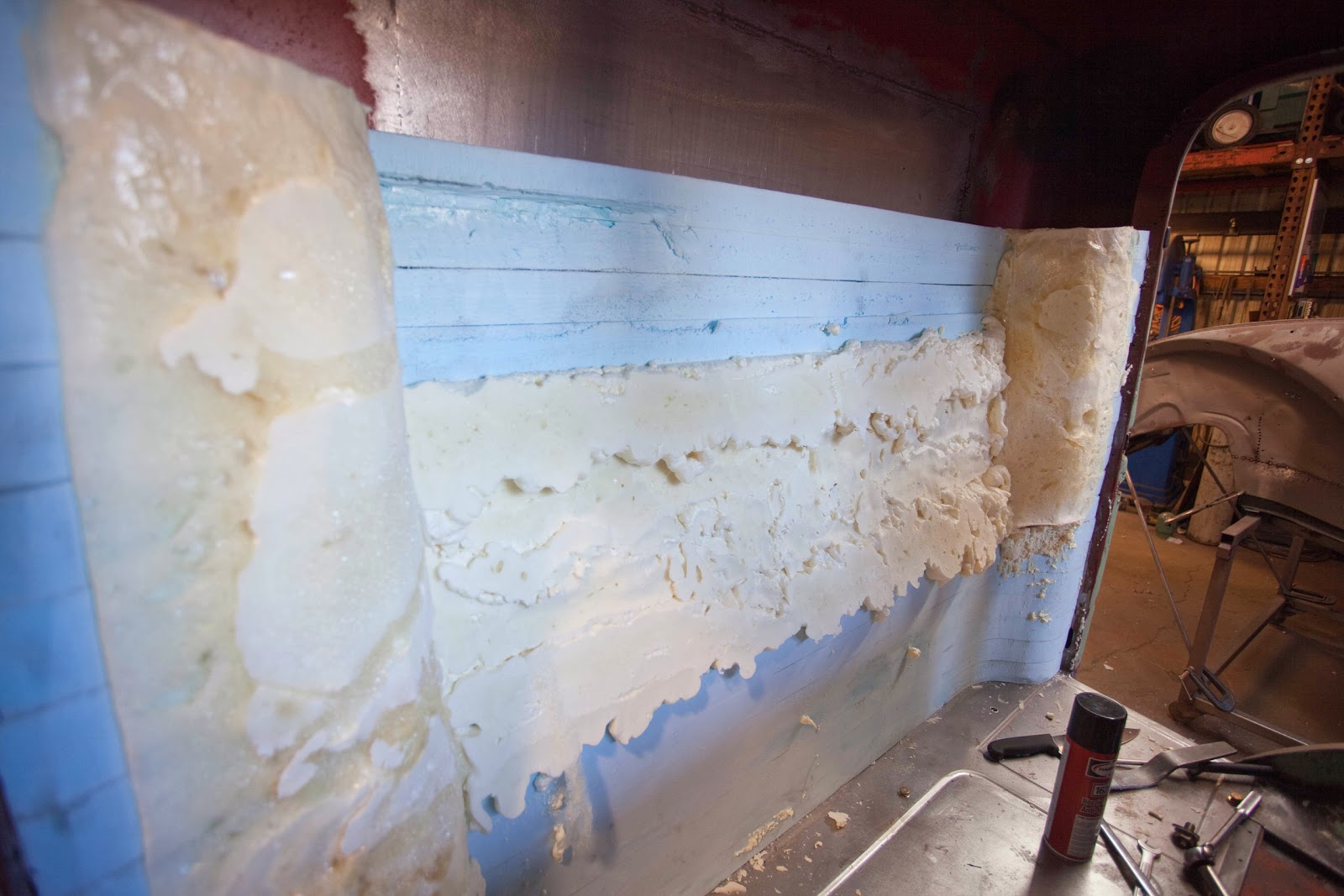 |
We used two inch foam insulation and cut out the basic shape and then glued them together with Scotch 77. I trimmed to much material off and had to use some spray foam to add back to the mold. If you can avoid this it will save you time and added grief. |
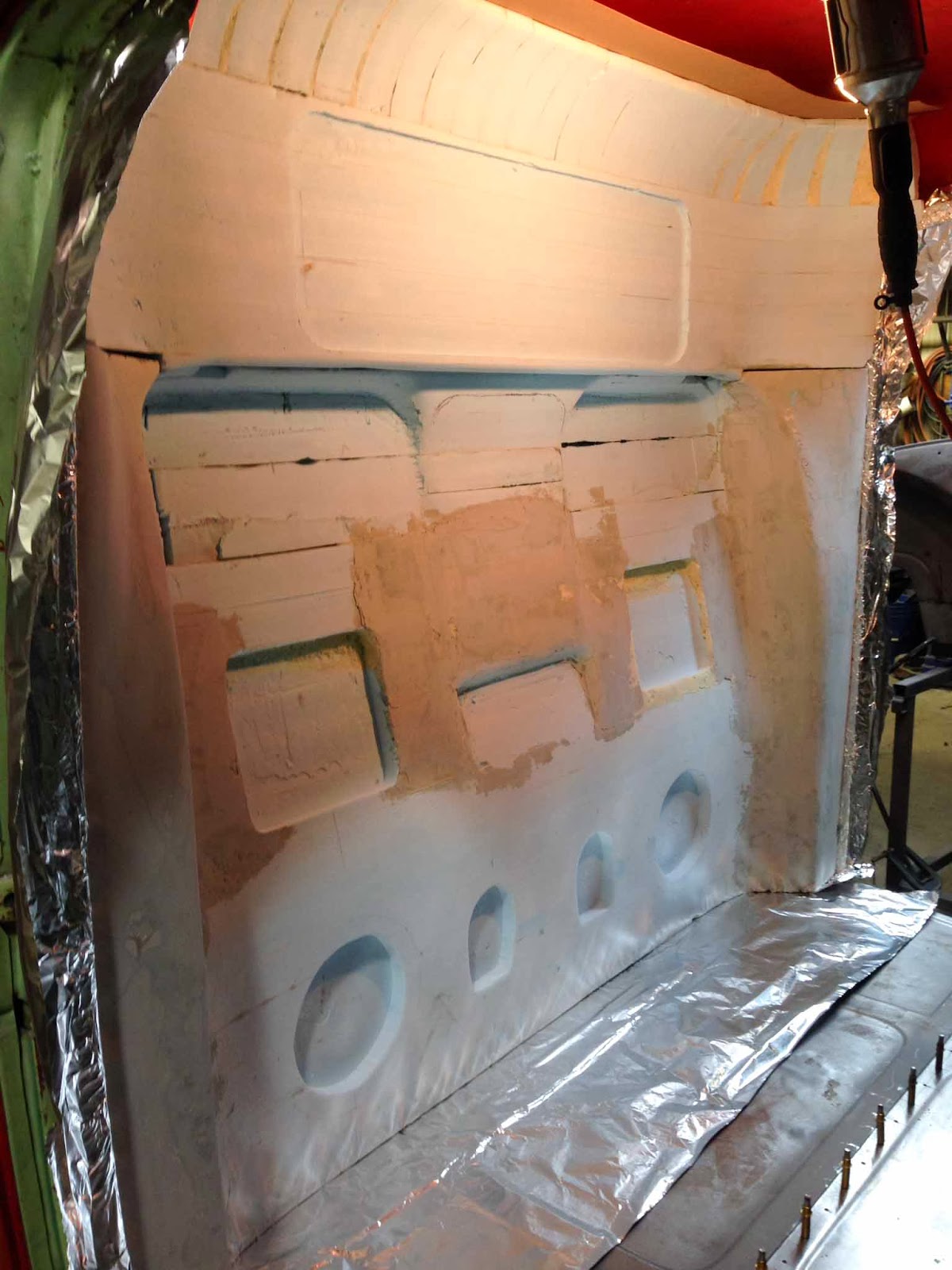 |
This is after all the carving and sanding was done. You always learn what you should have done different to make the job go easier and better after your done. Don't cut out to much material it took me about a week to fix those areas. I also would not of made the cut outs for the subs, amps, and crossovers in the mold. It made it hard to fiberglass these areas. If I was to do it again I would make it flat and cut them out later. |
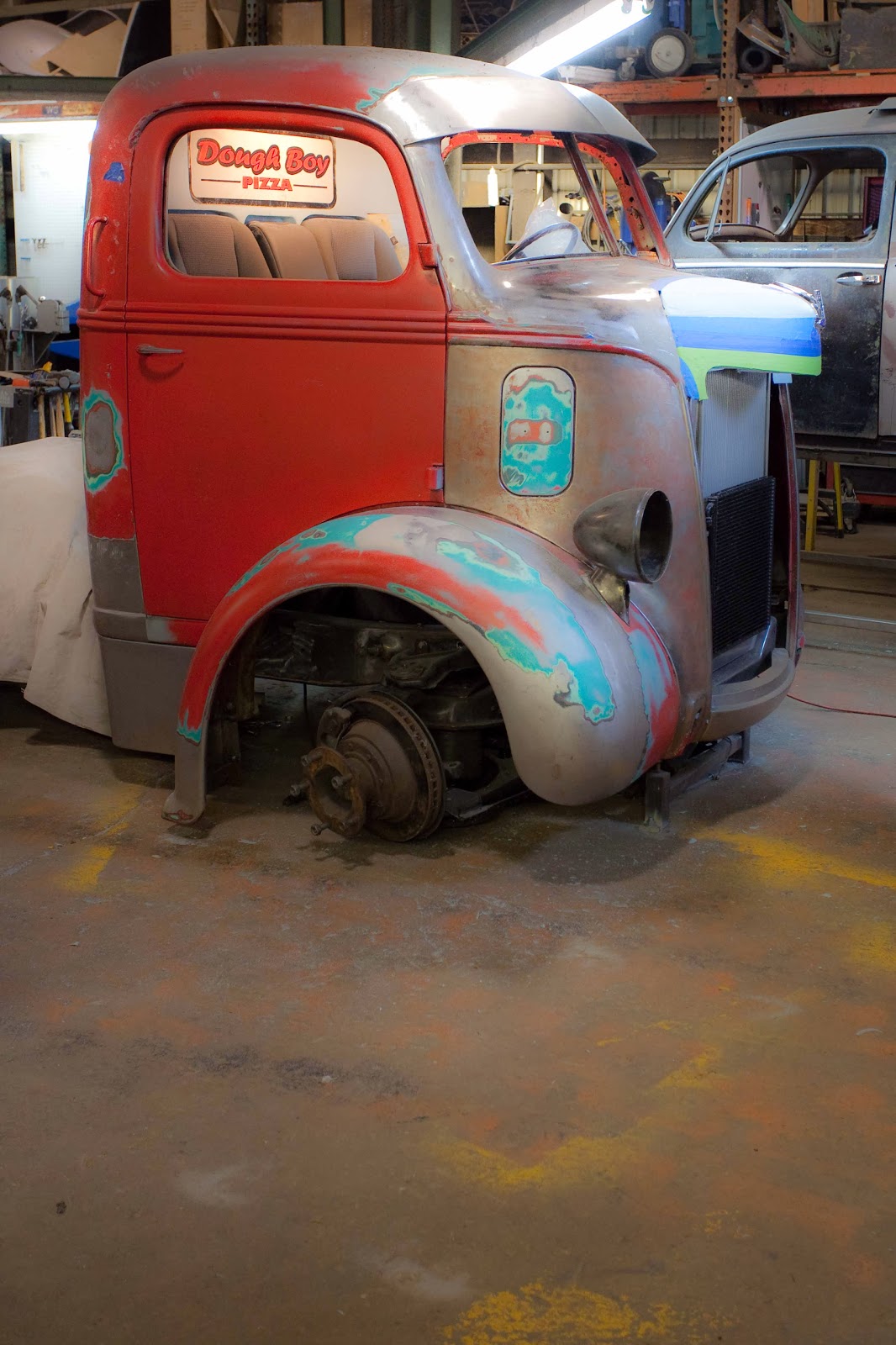 |
Test fitting of the mold before we start the fiberglass.The Dough Boy Pizza will be made out of aluminum and be bead rolled. |
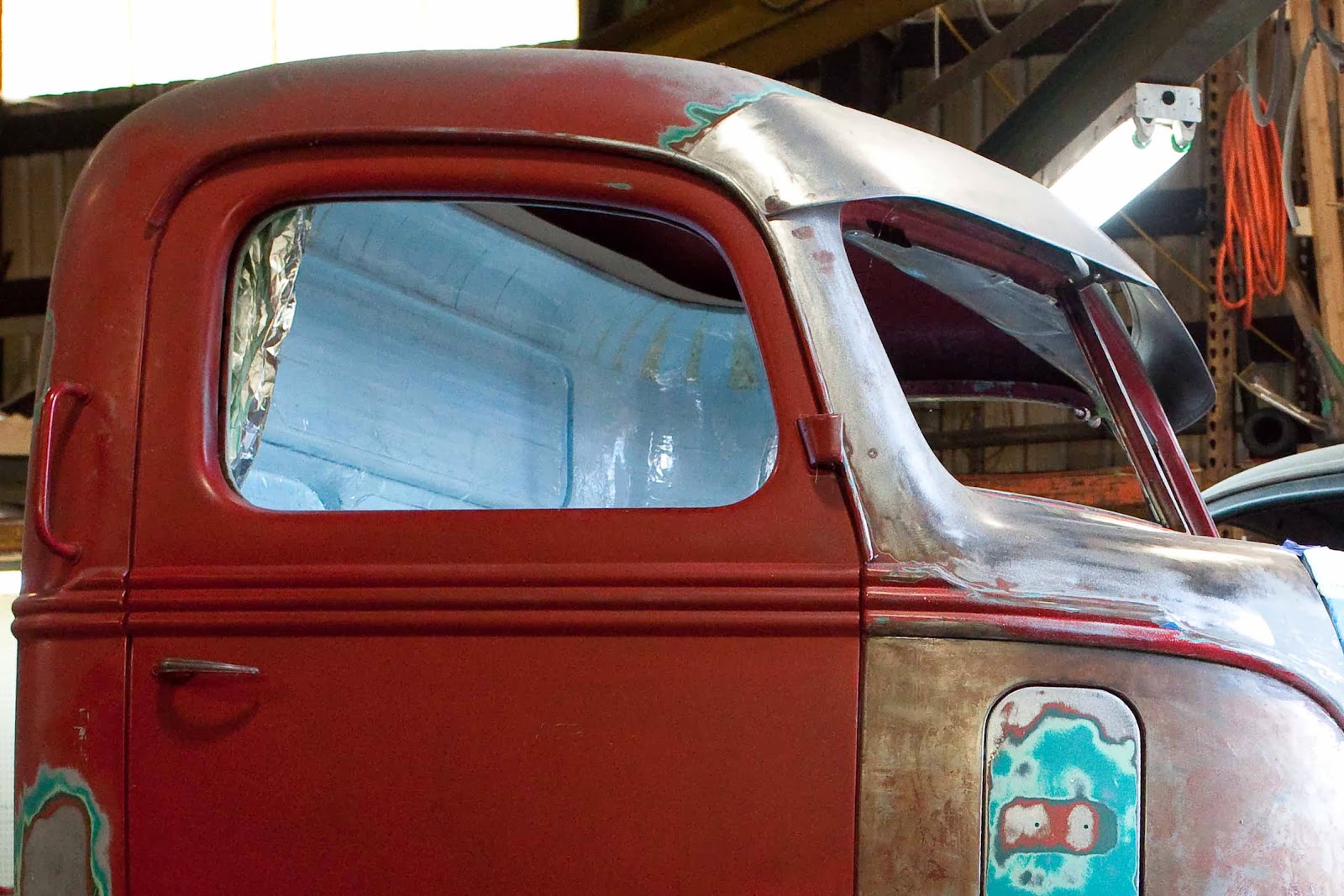 |
Before we fiberglass I used packing tape on the mold. This is so the fiberglass will release from the mold. |
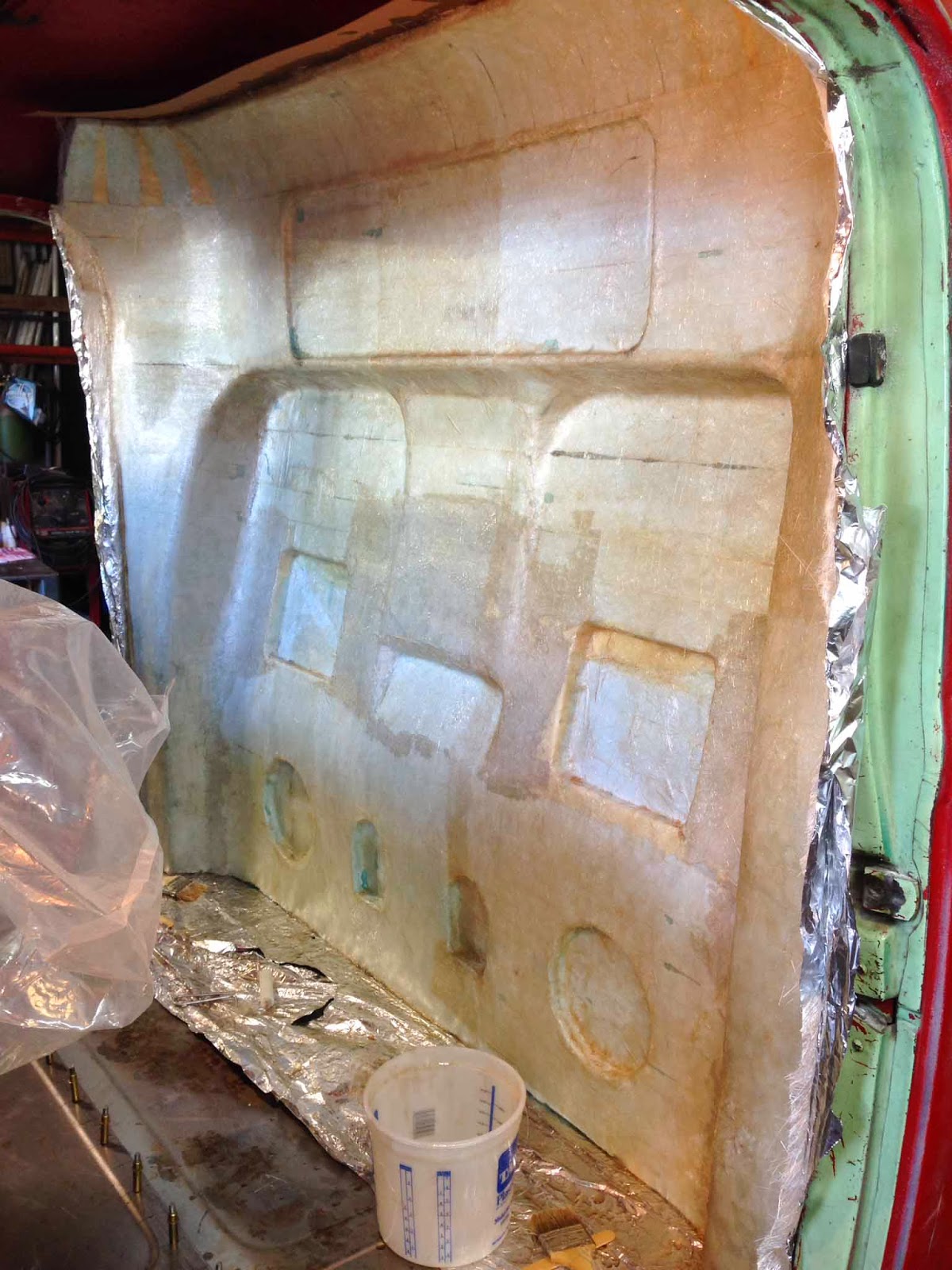 |
This is after the first layer of fiberglass. We did three layer. And this is when I remember why it had been thirty year since I used fiberglass. |
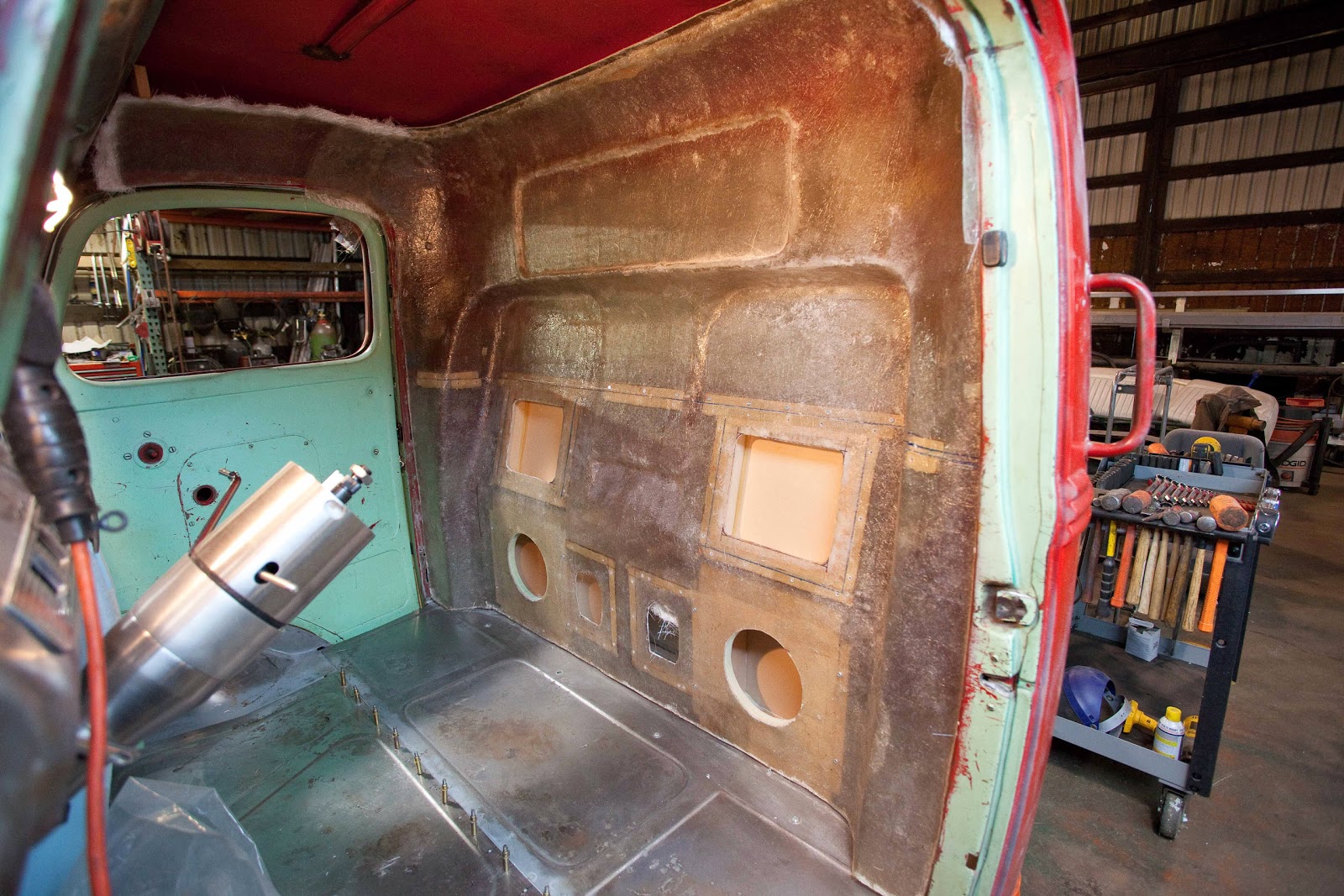 |
The part after the mold was removed. I made sub woofer enclosures and boxes for the amps and crossovers that attach behind the fiberglass. At this point I decided to make the top part out off fiberglass instead of a head liner. I think I'm getting addicted to the resin. |
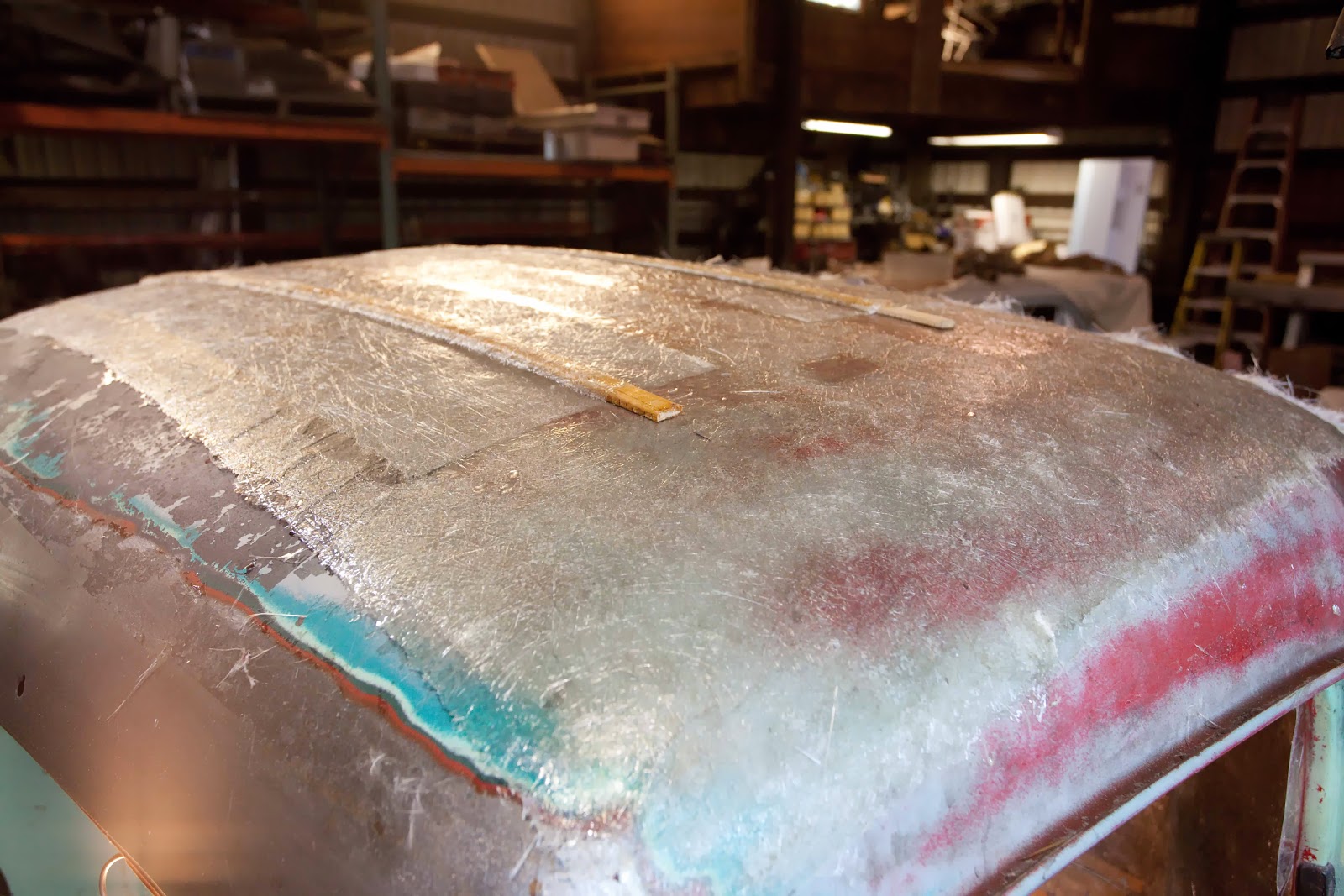 |
I used the top of the cab for the mold, and used packing tape as the mold release. Add two pieces of wood to give it some strength and a place to attach to the roof supports |
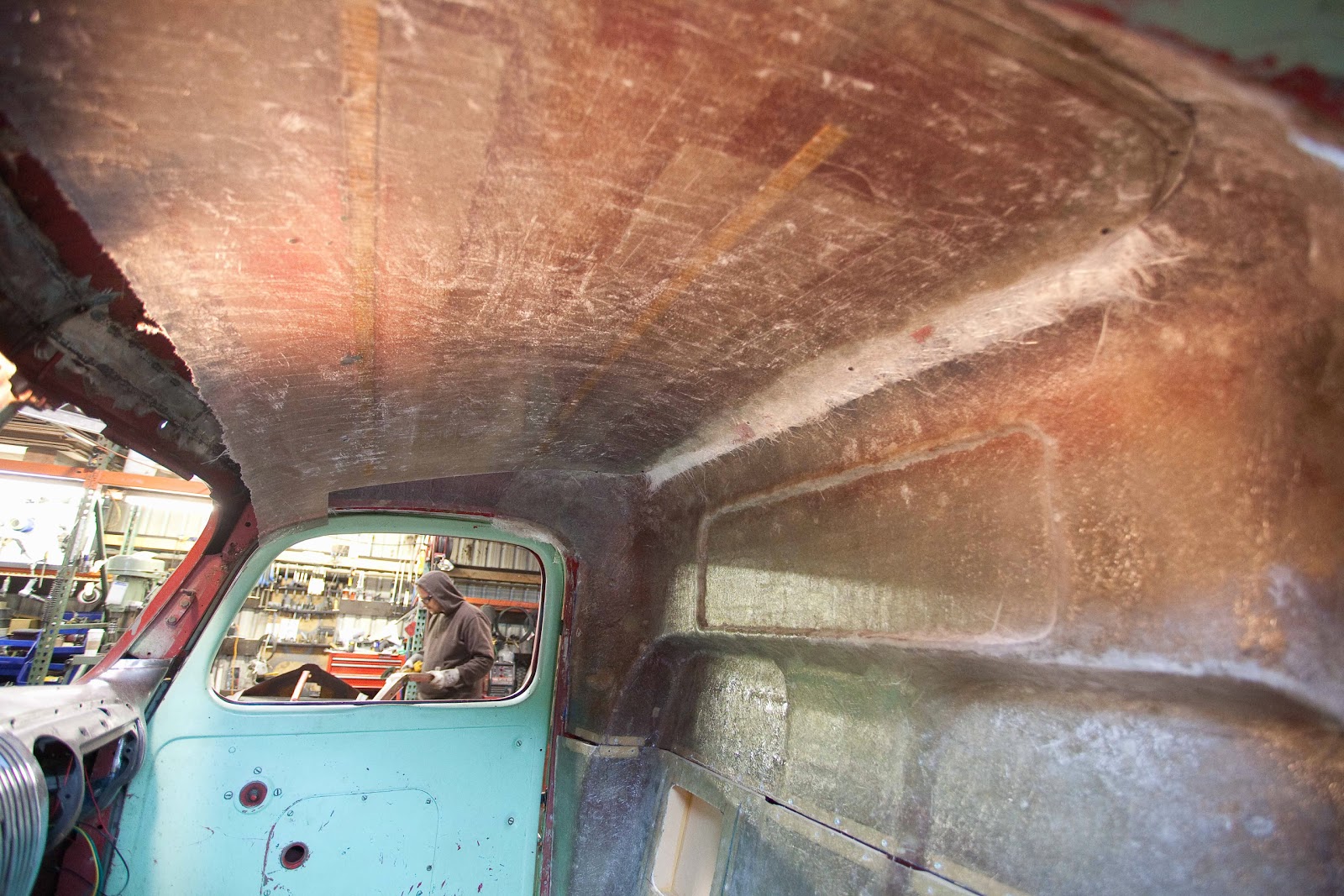 |
Test fitting before I add it to the rest of the part. |
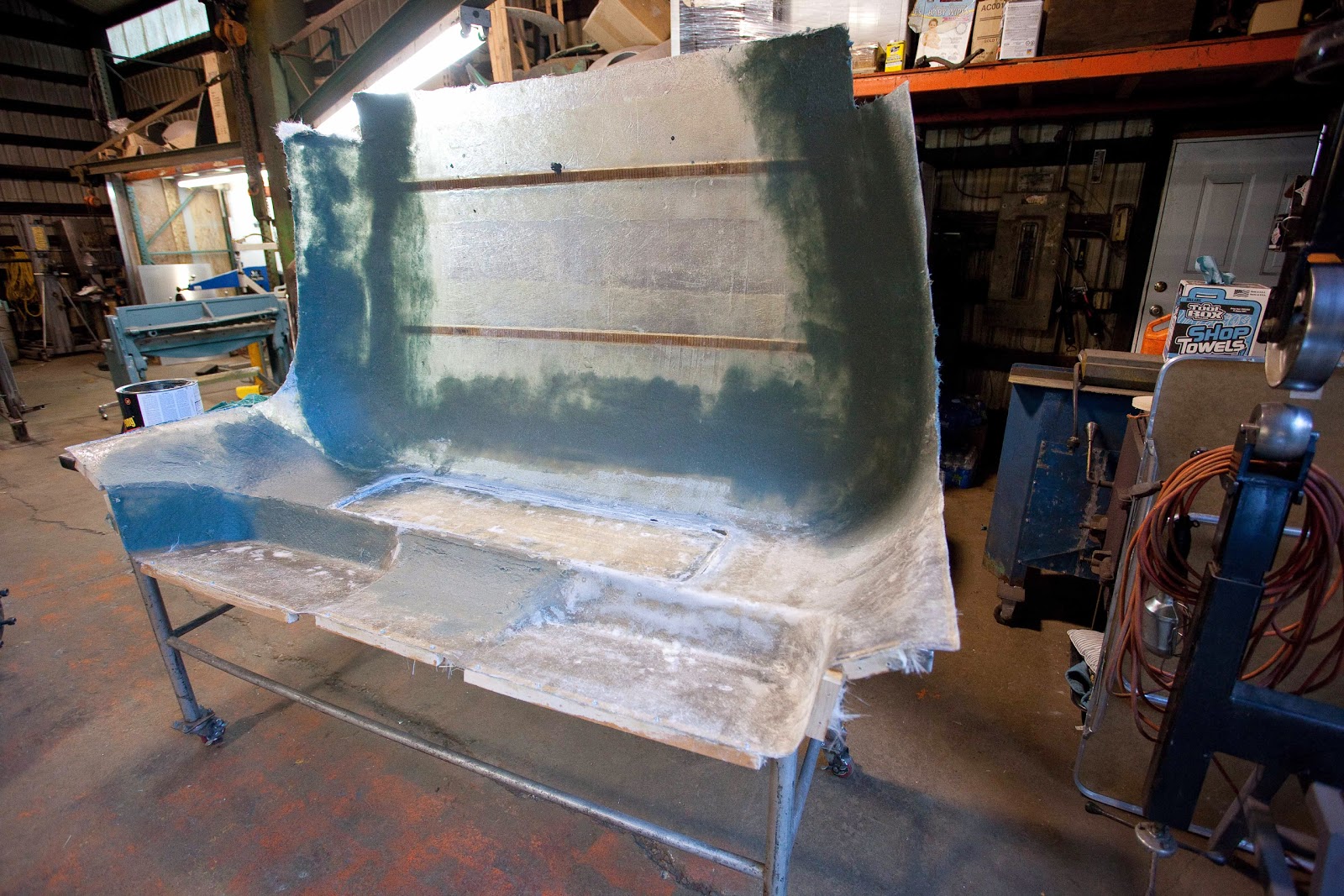 |
Working on smoothing it all out with some long and strong fiberglass filler. It will not have to be prefect, because the plan is that the part will be cover with some foam and the same materiel that the seats will be cover in. Just a little more fine tuning and one more test fit and this part will be complete. |